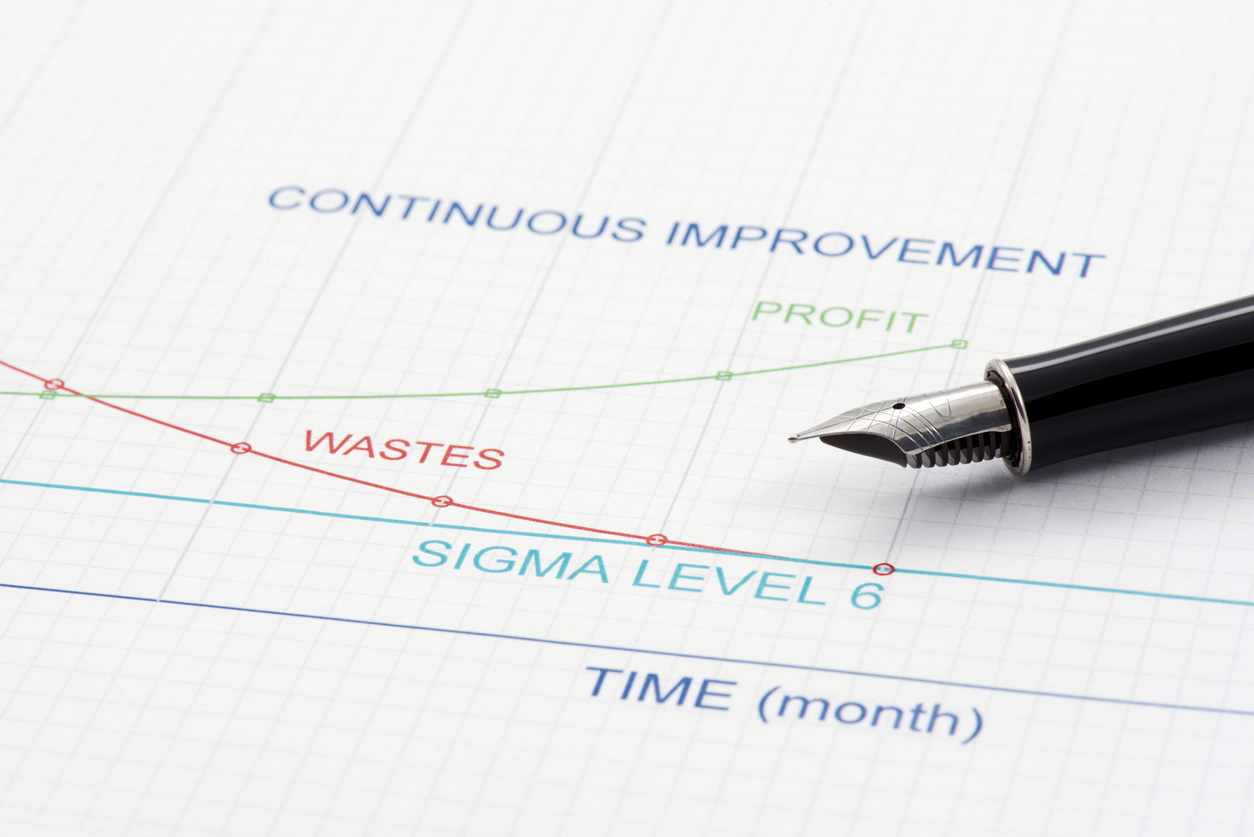
Lean Project Management Training
The same drive for efficiencies in manufacturing processes that sparked what is now known as “Lean” can help businesses reduce costs and decrease time-to-market while simultaneously boosting talent retention. The 2015 Lean Business Survey concluded that 92% of companies leveraging Lean enjoy “moderate to significant improvements in project success.” Growing your team’s Lean skill set can produce ongoing business benefits.
What Is Lean Methodology
Early 20th century car manufacturing, specifically Toyota factories in Japan, are widely identified as the origins of the Lean concepts around reducing waste and increasing output. In Womack and Jones’ book “Lean Thinking: Banish Waste and Create Wealth In your Corporation,” they summarize the five Lean principles born in the effort to make complex production lines more efficient:
- Precisely specify value by specific product
- Identify the value stream for each product
- Make value flow without interruptions
- Let the customer pull value from the producer
- Pursue perfection
One does not need to be in manufacturing to see that the motivation towards value, reduced interruptions, and customer engagement would be beneficial for any business. As Lean methodology was formalized over time, project managers across industries took note. In research papers published by the Project Management Institute, the advantages of Lean tools for managing projects are verified and project managers are encouraged to “reap the same kinds of benefits that Lean has achieved for manufacturing.”
What Is Lean Project Management
As its core, Lean methodology, tools, and techniques are grounded in a continuous improvement cycle in which how work is done is always viewed through the lens of opportunities be more efficient. To apply the Lean thinking to how to explain the methodology itself: reduce waste and increase value.
The improvement cycle is captured as: Define, Measure, Analyze, Design, and Verify. Project Managers can incorporate Lean thinking into their team’s work to cut waste, increase customer satisfaction, and even grow profit margins.
The Lean methodology does not replace Project Management tools. Rather, it is an enhancement that brings forward the importance of value throughout a project and creates opportunities to manage work more efficiently.
Project Managers that are trained in Lean:
- Understand the value creation process and how it connects to the business
- Identify and remove waste from the work process
- Adapt tools to meet the needs of a specific project t
The Project Manager that leverages Lean tools and techniques is better able to adjust for complexities and implement changes.
How Your Business Benefits from In-House Lean Practitioners
Companies with in-house Lean Practitioners enjoy more than just efficient work processes and outputs, there are positive talent impacts as well. Project Managers trained in Lean can be part of a larger company initiative of a continuous improvement culture that promotes “productivity, recruitment and retention.” In the data from 3,000 Lean Business Survey respondents, researchers identified 10 Benefits of Lean:
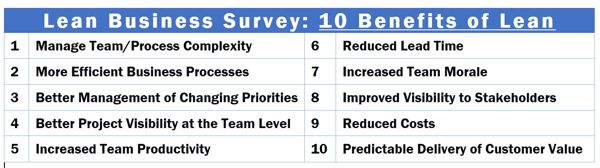
How To Get Your Team Started in Lean Project Management
If your company seeks a proven method for promoting quality and reducing costs, with the added potential benefit of a positive employee culture, Lean Six Sigma training should be pursued. Starting with the industry recognized Green Belt level, your Project Managers will learn how to:
- Initiate Six Sigma projects to bring about significant and lasting organizational change
- Formulate project selection criteria to focus Six Sigma initiatives on projects that will have the greatest chance of success
- Reduce waste and defects by applying Lean and Six Sigma principles
- Implement control charts to monitor how a process is performing over time
If your team includes those who have already begun their Lean training, consider enhancing their contributions to the continuous improvement work with Six Sigma Yellow Belt Training. With certified Lean experts on staff, your team or company will better be positioned to consistently realize cost savings in a culture that promotes adaptability and value.
About Megan Bell, MPM, PMP
A multi-hyphenate of corporate training, higher education, and creative agency work, Bell’s passion for connecting people to impactful information fuels an evolving career journey. Her portfolio includes conducting learning analytic research and reporting, managing a corporate mentoring program, authoring a blog series, facilitating leadership and career programs, serving on a non-profit board, and even occasional voice work. Bell’s education background encompasses UNC-Chapel Hill, Western Carolina University, and North Carolina State University.